tool monitoring system in cnc machine Caron Engineering's TMAC tool monitoring system for CNC machining optimizes tool cutting with high-precision sensors, a dedicated high-speed data processor, and an intuitive human . $34.99
0 · real time production monitoring
1 · real time machine monitoring
2 · machine run time tracking
3 · machine monitoring system for manufacturing
4 · fanuc mt linki software download
5 · fanuc cnc data collection
6 · cnc machine data collection
7 · best cnc machine monitoring software
$11.29
real time production monitoring
Tool monitoring leverages data from CNC machines to understand and predict the condition and lifecycle of the tool, reducing tooling and scrap part costs.MachineMetrics Tool Monitoring captures machine data straight from Fanuc .Caron Engineering's TMAC tool monitoring system for CNC machining optimizes tool cutting with high-precision sensors, a dedicated high-speed data processor, and an intuitive human .
Precise workpiece and tool measurement on a CNC machine helps to achieve accurate and consistent machining results, enhancing productivity, and minimising the risk of costly errors. Machine tool probes for workpiece setting .
real time machine monitoring
machine run time tracking
FANUC MT-LINKi and FANUC MT-LINKi Integration Server are fully scalable, out-of-the-box machine tool monitoring solutions that can monitor and manage data from one to two thousand machines. Operational and production data is . Tool condition monitoring (TCM) systems pave the way for automated machining through monitoring the state of the cutting tool, including the occurrences of wear, cracks, chipping, and breakage, with the aim of . The primary purpose of CNC production monitoring is to identify errors in the process and resolve them to get optimum efficiency. In this process, the monitoring interface .
System for Tool-Wear Condition Monitoring in CNC Machines under Variations of Cutting Parameter Based on Fusion Stray Flux-Current Processing . Antonino-Daviu J.A., Trejo-Hernandez M., Osornio-Rios R.A.A. Cutting Tool Wear Monitoring in CNC Machines Based in Spindle-Motor Stray Flux Signals. IEEE Trans. Ind. Inform. 2020:1. doi: 10.1109/TII .
Complete systems for tool monitoring and process control for all types of metal cutting machine tools. Control-integrated tool monitoring for open CNC control panels; Sensors for monitoring micro tools; Integrated acoustic work piece dimension control .Modern solutions imply using the cloud services, in particular, based on cloud infrastructure and a machine tool health forecasting system based on analytics [10, 11]. A service channel that provides synchronized communication between the CNC machine tool and the remote service platform (Fig. 1) supplements the control system of each machine tool.This paper is sponsored by the “ Technology of on-line monitoring system for thermal characteristics of NC machine tools ” (No. H2019304021); The “ Project funded of Shanghai science committee-Precision technology and its application for five-axis machine tool based on the real-time compensation ” (NO.
What is CNC machine monitoring? CNC machine monitoring refers to software that tracks the performance and activity of CNC machines in real-time. CNC machine monitoring helps manufacturers reduce production downtime, improve quality control, boost production speed, and better optimise production schedules. SPC Innovations Detector Type 202 broken tool sensor installed in a single-spindle CNC machine. (Photograph courtesy of SPC Innovations.) PCS Positive Contact Tool Monitor from TPS International, installed on a transfer machine. . A laser tool monitoring system, such as the LaserControl NT from Blum LMT, Erlanger, Ky., can measure the length .
large metal window box
Detect broken tools, check for part removal and more with a tool breakage detection system (Positive contact sensor). Tool breakage detection and monitoring systems can save companies huge costs in many areas including scrap parts, downtime, setup time, part inspection as well as repair and maintenance costs from crashes which could have been avoided with a positive .
Big Data Oriented Smart Tool Condition Monitoring System,” IEEE Transactions on Industrial Informatics, vol. 16 . CNC Machine Tool Wear Monitoring Based on Densely Connected Convolutional Networks,” in . Proceedings - 2020 Prognostics and Health Management Conference,Complete systems for tool monitoring and process control for all types of metal cutting machine tools. Control-integrated tool monitoring for open CNC control panels; Sensors for monitoring micro tools; Integrated acoustic work piece dimension control . TMAC 3.0 has been completely redesigned with an intuitive streamlined user-interface that offers numerous configurations for viewing tool monitoring and sensor data. The TMAC system processor now houses its own web server, making the HMI (human-machine interface) browser-based, which enables real-time monitoring from any network connected . Intelligent manufacturing as the development direction of the new generation manufacturing system has become a hot research topic. Computer numerical control (CNC) machine tools are the core manufacturing equipment in discrete manufacturing enterprises, collecting and monitoring the data is an important part of intelligent manufacturing workshops.
Thus, a reliable tool condition monitoring system integrated with data analytics and IoT using cutting signals is expected to be more efficient for smart CNC machines than conventional cutting chatter monitoring systems, as shown in Fig. 1 [11].Caddis can be installed onto any type of CNC machine within minutes with either a stack-light, Wi-Fi, cellular or ethernet model to provide you with critical real-time manufacturing analytics related to uptime, preventative maintenance, utilization, excessive downtime, temperature and vibration.CNC Machine operators can easily access this data from any type of device and .
2.2 Assembly of Toolholder On-Rotor Sensing. To maintain the original milling machine tool handle structure and not weaken its strength, the sensing unit is installed on the cutter arbor shown in Fig. 1.At the same time, to reduce the influence of static centrifugal force generated by spindle rotation, an inner ring with an inclined plane is designed in this scheme, as shown in . For many years, machine tools have been the backbone of many manufacturing industries. Machine tools also play an important role in the global economy nowadays. These machines, which transform complex designs into . This paper introduces remote monitoring and maintenance system for machine tool manufactures. The system uses mobile phone unit as a communication method between customer and machine tool manufacture to realize and install this system at the customers’ site easily. This system already installed for more than 10,000 machine tools.
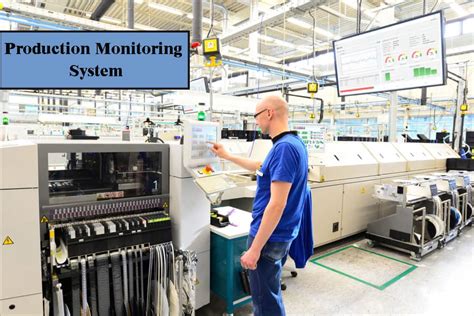
A framework of general machine tool monitoring system with four layers is proposed and several key stumbling blocks are researched, such as heterogeneous machine data acquisition, data analysis, and related application. . Zhang X, Li Y, et al. Open CNC machine tools state data acquisition and application based on OPC specification. Procedia .
A foundational report of global machine tool market that was issued in 2019 announced that spindle systems of CNC machine tools are increasingly important than ever for that the even distinguished .
The computer numerical control (CNC) machine has recently taken a fundamental role in the manufacturing industry, which is essential for the economic development of many countries. The "CNC Machine Tool Monitoring System Market" is expected to reach USD xx.x billion by 2031, indicating a compound annual growth rate (CAGR) of xx.x percent from 2024 to 2031. The market was .
FANUC MT-LINKi Machine Tool Monitoring Software. FANUC MT-LINKi and FANUC MT-LINKi Integration Server are fully scalable, out-of-the-box machine tool monitoring solutions that can monitor and manage data from one to two thousand machines. Operational and production data is monitored and collected using a PC and an Ethernet connection. A variety of data points are .Buy broken tool detection devices and parts. Quality issues and scrap parts are major costly problems that can be eliminated by broken tool monitoring. Our PCS-100 can detect broken tools and be installed on any CNC including transfer lines, screw machines, drill machines and even used for detecting parts or checking the removal of a part. Tool wear monitoring and real-time predicting tool life during the machining process is becoming a crucial element in modern manufacturing to properly determine the ideal point to replace tool, remains a challenge currently. In this paper, the model approach for in-process monitoring and predicting progressive tool wear by using machine vision is proposed. .Harmoni is the #1 solution for real-time machine data collection - everything from machine monitoring, OEE, & labor & job data collection via RFID.
The digital twin is driving the machine manufacturing and processing workshop to change in the direction of digital intelligence and service. Aiming at the application requirements of virtual simulation monitoring of typical CNC machine tools for the unified interaction and integration of processing and production process data, this paper proposes a development .A CNC machine monitoring system that automatically collects and archives CNC machine data is key to creating a manufacturing process that benefits from machine software. A CNC machine monitoring software platform allows for the real-time visualization of CNC machining job status and can be used as an integral part of any manufacturing .
Modern CNC machine monitoring systems collect real-time data from machines, providing insights into various performance metrics such as spindle speed, feed rate, tool usage, and machine status. This data is analyzed to detect anomalies, predict maintenance needs, and optimize machine parameters, ensuring consistent and high-quality output.
machine monitoring system for manufacturing
$44.55
tool monitoring system in cnc machine|best cnc machine monitoring software